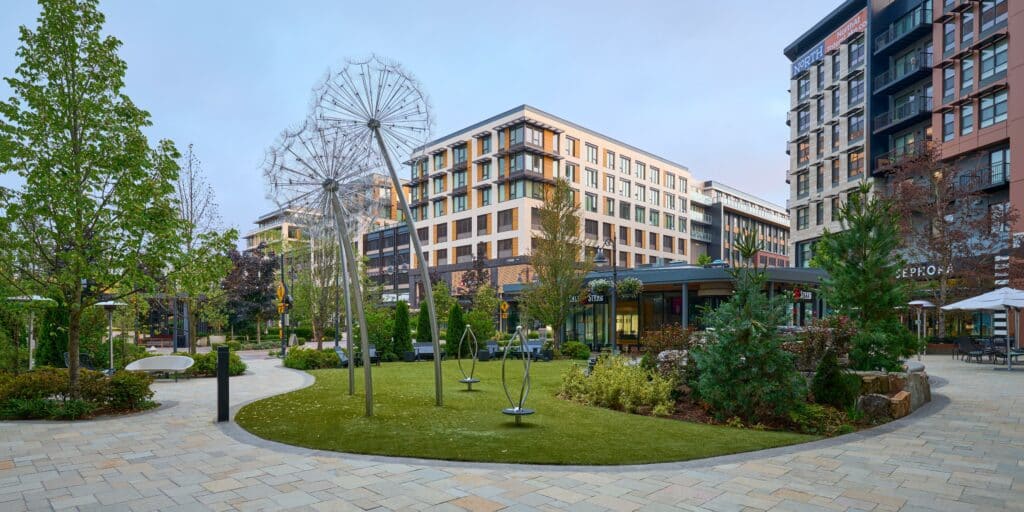
At Robinson Construction Co., we recognize that the cornerstone of every successful construction project lies in meticulous planning and efficient lead time management. The term ‘lead time’ describes the total duration from ordering materials and equipment to their arrival on-site. Effective lead time management directly impacts your project’s progress, timelines, and budgets, significantly influencing overall project success.
Understanding Lead Time in Construction
Lead time significantly impacts the efficiency and effectiveness of any construction project, including commercial and multifamily construction. Whether installing a roof or acquiring specialized construction materials, the time it takes to procure these items varies greatly based on factors like manufacturing time, supplier capacity, and global market conditions.
Why Lead Time Matters
Efficient construction demands a thorough understanding of lead time. Robinson Construction Co. prioritizes accurate forecasts and proactive planning to mitigate potential delays, increased costs, and disruptions in project schedules. Prior to the pandemic, lead times were generally shorter and more predictable. However, today’s supply and demand fluctuations have resulted in extended lead times becoming commonplace across many industries.
Factors Contributing to Long Lead Times
Supply Chain Disruptions
Supply chain disruptions, notably highlighted during the pandemic, significantly affect the availability of materials. These disruptions necessitate early procurement and clear communication within your supplier network to minimize impacts.
Customization and Specialized Requirements
Customization frequently results in longer lead times. Complex or highly customized components take longer to manufacture, making it essential to account for extended lead times when developing your project schedule.
Regulatory and Permitting Delays
Permitting processes and regulatory compliance can considerably extend lead times. Early engagement in permitting procedures is critical to keeping your project timeline accurate and realistic.
Strategies for Reducing Lead Times
Advanced Planning and Scheduling
Efficient manufacturing and reducing lead times begin with proactive planning and scheduling. Robinson Construction Co. employs robust project management software solutions and tracking systems to streamline material orders and mitigate delays in material lead times.
Strong Supplier Relationships
Developing strong relationships with suppliers ensures that “communication happens earlier,” identifying and addressing issues before they affect project efficiency. Ryan Reese from Alder’s Architectural Sales emphasizes this proactive approach, ensuring clients aren’t burdened by unexpected delays.
Effective Inventory Management
Robinson strategically manages inventory, balancing availability and cost efficiency. This approach directly supports efficient lead time management by reducing holding costs and minimizing the risk of material shortages.
Contingency Planning
Robinson consistently incorporates comprehensive contingency plans, preparing for potential challenges and external factors such as quarantine restrictions, price increases, or unexpected supplier delays.
The Importance of Efficient Lead Time Management
Efficient lead time management is crucial for project execution. Robinson’s tailored management solutions ensure your project timeline can accommodate potential delays, ensuring smooth progression through every phase of construction.
By effectively managing lead times, Robinson significantly reduces labor costs, avoids workflow disruptions, and ensures projects are completed on time and within budget, demonstrating our expertise in supply chain management.
Proven Approaches Robinson Uses for Project Success
Robinson Construction Co. has consistently delivered exceptional results by strategically managing lead times. Our proven methodologies include:
- Precise forecasting and advanced planning
- Early team involvement and clear communication
- Leveraging sophisticated software solutions for inventory management
- Direct collaboration with suppliers to anticipate and swiftly resolve issues
Real-World Examples of Effective Lead Time Management
Robinson’s successful management of lead times can be seen through our diverse project portfolio, including:
Mixed-Use Development: The Village at Totem Lake
This major redevelopment project required extensive scheduling and management of long lead items. Through meticulous planning, Robinson ensured materials arrived as scheduled, maintaining project timelines without disruptions.
Costco Wholesale Projects
Robinson successfully managed multiple retail projects for Costco Wholesale, showcasing our ability to manage tight schedules, specialized materials, and complex logistics, resulting in timely project completions.
Educational Institutions: Beatrice Morrow Cannady Elementary School
Managing extended lead times for customized construction materials was vital for this school project. Robinson’s detailed planning allowed the project to progress smoothly, minimizing potential delays.
Navigating External Factors
Robinson understands that external factors, such as economic conditions, global pandemics, and international supply chains, significantly influence material availability and lead times. Our proactive approach to managing these variables includes:
- Continuous market monitoring
- Adaptable scheduling techniques
- Risk mitigation strategies that prepare for potential disruptions
Frequently Asked Questions (FAQ)
What exactly is lead time in construction?
Lead time encompasses the entire duration from ordering materials or equipment until their delivery to the construction site.
Why do longer lead times occur?
Longer lead times result from supply chain disruptions, material shortages, increased customization, and delays in regulatory approvals and permits.
How can lead times impact my construction project?
Extended lead times can lead to project delays, budget overruns, increased labor costs, and disruptions to your project schedule.
What strategies does Robinson use to manage lead times effectively?
We employ proactive forecasting, strong supplier relationships, sophisticated inventory management software, and contingency planning.
Why is early procurement critical?
Early procurement ensures materials arrive as planned, reducing the risk of delays and facilitating smooth project execution.
How does Robinson ensure clear communication about lead times?
Robinson emphasizes transparent, ongoing communication with clients and suppliers to promptly address any lead-time-related issues.
Take Action Today
Set your project on the path to success with Robinson Construction Co. Our expert team proactively manages lead times, ensuring your project stays on track and within budget. Reach out to us today to discover how our meticulous planning and advanced management strategies can deliver exceptional results, keeping your project efficient, timely, and successful.